A workplace like no other: Making the world's largest telescope mirrors
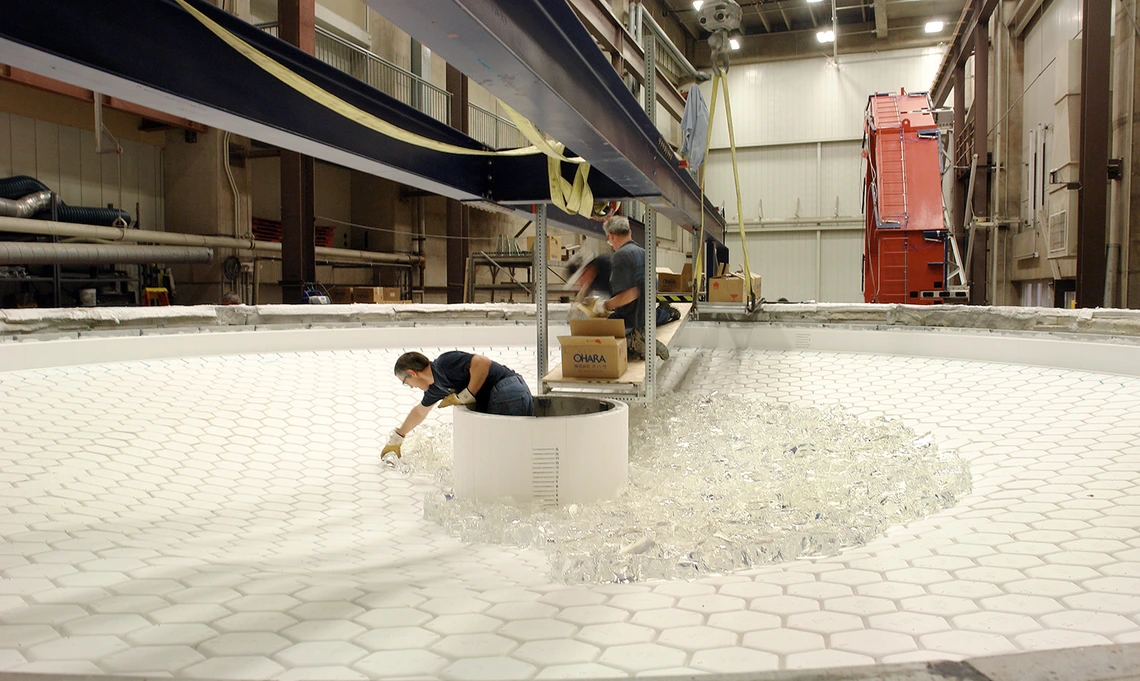
Technicians at the Richard F. Caris Mirror Lab load chunks of glass onto the honeycomb mold during fabrication of Rubin Observatory’s combined primary/tertiary mirror. The mirror measures nearly 28 feet (8.4 meters) across.
Richard F. Caris Mirror Lab

Buddy Martin stands in front of the large polishing machine, or LPM, at the Richard F. Caris Mirror Lab
Richard F. Caris Mirror Lab
When "the greatest astronomical discovery machine ever built" released breathtaking new images of space in June, the dedicated team of University of Arizona engineers, technicians and scientists who helped make it happen could finally celebrate the culmination of decades of work.
Tucked underneath Arizona Stadium, the Richard F. Caris Mirror Lab was a key partner in building the world's largest telescope for the new Vera C. Rubin Observatory in Chile. On June 24, the observatory released its first spectacular images: glowing nebulas, pulsating stars, swarms of asteroids and millions of galaxies. The observatory will scan the southern sky nightly for the next 10 years and expects to uncover a "treasure trove of billions of scientific discoveries.”
A milestone decades in the making
The Rubin's giant, 28-foot mirror was made at the Mirror Lab, which is the only place in the world with the optics manufacturing facility that can make mirrors at that scale, according to veteran Mirror Lab project scientist Buddy Martin.
For Martin, Rubin's sharp images are a testament to the exceptional quality of the mirrors and the perfect alignment of optics inside the telescope.
"All of us at the Mirror Lab are thrilled to see these images, to see this project come to fruition," he said. "Something like this doesn't happen every year – or even every decade – in our line of work."
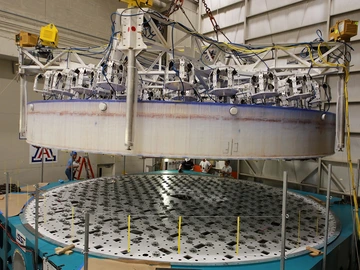
The Rubin Observatory's Primary/Tertiary Mirror (M1M3) is lifted into its transport/storage container using a custom vacuum lift.
RubinObs/NOIRLab/SLAC/DOE/NSF/AURA
Reinventing telescope mirrors
Founded in the 1980s and driven by the visionary Roger Angel, Regents Professor of Astronomy and Optical Sciences, the Mirror Lab pursued a new way of manufacturing mirrors that broke with the centuries-old tradition of carving telescope mirrors from solid discs of glass.
The Mirror Lab developed a unique honeycomb design that allows for large, lighter-weight mirrors that still offer maximum mechanical rigidity, traits that used to be considered mutually exclusive.
How to make the world's largest mirrors
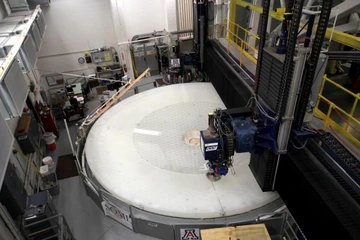
Polishing the mirror's surface takes about two years, requiring frequent optical tests and adjustments of the lap assembly.
Richard F. Caris Mirror Lab
Each mirror begins as 20 tons of glass chunks shipped from Japan and delivered to the Mirror Lab on semitrucks. The chunks are then unpacked and inspected before Mirror Lab technicians and engineers load them into a fire-engine-red, custom-designed rotating furnace. A precise, computer-controlled process then heats the glass chunks until they melt.
About 25 full-time employees work at the Mirror Lab, which, in addition to the furnace, features a grinding machine, a polishing machine and a test tower standing 100 feet tall.
"We work in shifts, and when needed, we can work on the mirrors 24/7," Martin said, explaining that many processes are largely automated. "Still, we do intervene and make adjustments in the schedule. There are human eyes on the monitor the entire time."
Once the mirror is cast and cooled to room temperature, a crane lifts the furnace lid and technicians disassemble the side walls, exposing the mirror, which is then hoisted upright and placed in the "wash-out stand." Using high-pressure washers, the techs then spend several days blasting the mirror's back side to wash out the ceramic fiber cores that made up the honeycomb mold.
Next, the mirror is lifted onto the "large optical generator," where a diamond wheel quickly moves around the mirror's top and edges, grinding away at the glass and defining its surface to an accuracy of about 25 micrometers – roughly a third of the diameter of a strand of human hair.
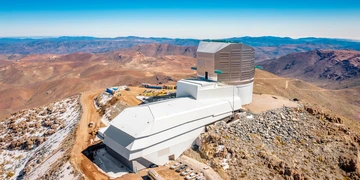
The Vera C. Rubin Observatory, located on a mountaintop in Chile, will revolutionize the way astronomers explore the cosmos. Using the largest camera ever built, Rubin will repeatedly scan the sky for 10 years and create an ultra-wide, ultra-high-definition, time-lapse record of the universe.
To move mirrors around the lab, the technicians place them onto giant supports that glide across the smooth floor on a cushion of compressed air, not unlike pucks on an air hockey table. Polishing the mirror is the most time-consuming step in the mirror-making process, taking about three years to be completed as it slowly rotates on the "large polishing machine."
The mirror is polished to become shiny and transparent, while also needing to have the shape correct to an accuracy of 25 nanometers, or 1 millionth of an inch. To achieve this level of precision, the engineers and technicians work in small increments, moving the mirror back and forth between the large polishing machine and the testing tower, where its surface is scanned with red laser light.
"This gives us a contour map of the mirror's surface," Martin said. "Based on those data, we design the motion of the tool so that it's going to rub on the high spots."
From there, the mirror goes back to polishing and testing. In all, it may take 50 to 100 iterations to achieve the required accuracy.
It's not a job for those who are in a hurry and only have an eye on the finish line.
"To work here, you have to enjoy the process, not just the results," Martin said, adding that he likes "the everyday math problems" of his job the most (and writing reports the least). "Nobody could stand this if they only cared about the results and had to wait a decade or more to see them. You have got to enjoy what you're doing day in and day out.
Mirror Lab at a glance:
- Founded in the 1980s
- About 25 full-time employees
- Created a 28-foot-wide mirror for the world's largest telescope
- Each mirror begins as 20 tons of glass chunks
- It takes an average of 3 years to polish each mirror
- Surface must be accurate to the scale of 25 micrometers – roughly a third of the diameter of a strand of human hair