Q&A: Turning glass into cosmic discoveries

After casting, the mirrors are placed in a vertical support structure. (Photo by: Damien Jemison/GMTO Corp.)
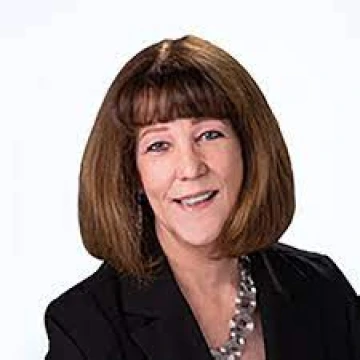
Cathi Duncan, senior program coordinator, Steward Observatory
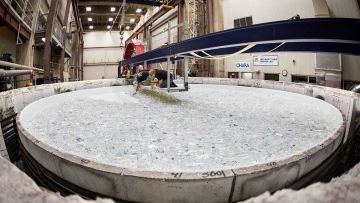
Workers at the University of Arizona's Richard F. Caris Mirror Laboratory place glass in the furnace for the fifth mirror for the Giant Magellan Telescope.
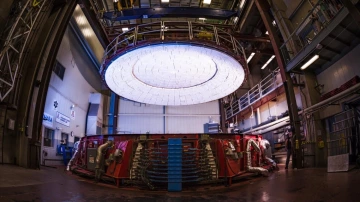
Glass is melted inside a rotating furnace, shown here with the lid suspended from an overhead crane. (Photo by: Damien Jemison/GMTO Corp.)
Tucked away beneath Arizona Stadium, the Richard F. Caris Mirror Laboratory is a place unlike any other. Under the skilled touch of technicians and the precision of one-of-a-kind machinery, chunks of glass become giant mirrors for some of the world's largest and most ambitious astronomical observatories.
The Mirror Lab just completed a major milestone in the search for other, potentially Earth-like planets and the exploration of the universe, with the casting of the final required primary mirror for the Giant Magellan Telescope, or GMT, which will peer farther into the cosmos and further back in time than any telescope before it.
In this Q&A, Cathi Duncan, senior program coordinator for Steward Observatory, discusses the unique work being done at the lab.
What makes the Richard F. Caris Mirror Laboratory so unique?
We are the only university – actually the only place in the world – that has such a facility. Nobody else produces mirrors this size, using our signature spin-casting process. We make 8.4-meter mirrors, 28 feet in diameter. They're made from 20 tons of glass, yet extremely lightweight at their size, because they are 80% hollow. Regents Professor Roger Angel, who founded the Mirror Lab, came up with the idea that if you pour molten glass over a honeycomb mold, it will form a mirror that is lightweight yet extremely stiff and rigid once you remove that mold. Prior to the 1980s, telescope mirrors were made by grinding out thick, solid disks of glass. That was an issue because if they got too big, they would break under their own weight. So, in order to make bigger telescope mirrors, astronomers had to think of a way to overcome that restriction.
Can you walk us through the process of casting a mirror?
First, you have to create the mold that will give the mirror its honeycomb structure. For an 8.4-meter mirror, you need 1,700 mold cores, and you have to make sure they're bolted in correctly and the position of each one is measured correctly. It takes months to get that done. Then we bring in the glass – 20 tons of E6 borosilicate glass made exclusively for us by Ohara Glass Corp. in Japan. That's four semitrucks carrying 68 crates. Each crate has 24 cases in it. Each piece of glass has to be cleaned, weighed and inspected by hand. All that glass is loaded on top of the mold cores. Then the lid goes down on our rotating furnace and we turn it on. It takes about five days for the glass to heat up to 2,100 degrees Fahrenheit. At that point, it is like molten lava flowing down through the mold. With GMT No. 7, it took five days to heat the oven to its peak temperature, and that was on Oct. 7. Five hours later, we started the cooling process, or annealing, during which the atoms in the glass take their final positions. The mirror should reach room temperature on Dec. 30, and then we can remove the lid, take the mirror blank out and begin power-washing all the mold material away. Once finished, the mirror is ready to be polished.
How does the polishing work?
Our polishing machine is run by computers and it removes glass selectively as it goes around the mirror surface. We are very conservative, so we don't over-polish, which would be a problem. After about a week or 80 hours of polishing, we move the mirror underneath our 90-foot-tall test tower and perform laser interference testing. Essentially, the mirror is scanned with a laser to create a topographical map, if you will, of the surface. The results are then programmed into the computer system and it will run the polishing until the next testing session. And we do that over and over and over again. It can take three years to polish it to the desired smoothness and accuracy, which is within nanometers.
What does a typical day in the Mirror Lab look like?
Approximately 35 people work here, primarily technicians and engineers, on a morning and an evening shift. We have a casting crew, a polishing crew and a third crew that is responsible for integrating mirrors into their fixtures once they have been shaped and polished. Right now, our casting crew is busy with the GMT No. 7, the final mirror segment for the GMT. Our polishing people are working on the front surface of a 6.5-meter mirror, the backside of another mirror of the same size. Once they are done, sometime next year, they'll start working on the fifth mirror for the GMT. Some of our people are now retiring, so we have new staff coming in and transferring that important knowledge over to them.
Can you give us a brief history of the Mirror Lab? How long has it been here?
Obviously, we didn't start with a giant 8.4-meter mirror. The first mirror, made in 1985 by Dr. Angel, measured 1.8 meters, or 6 feet across. It is now being used by the Vatican Observatory up on Mount Graham, and they just celebrated their 30th anniversary in September. That telescope is doing some very exciting science at this point. We then went to 3.5-meter mirrors, then to mirrors twice that size, and ultimately the 8.4-meter mirrors. Over the last 38 years we have produced 24 mirrors, and we have a few more to go. The 6.5-meter mirror of the MMT, formerly known as the Multiple Mirror Telescope, which is on Mount Hopkins south of Tucson, was made here. We also made the two 8.4-meter primary mirrors for the Large Binocular Telescope on Mount Graham – currently the most advanced and largest single-mount mirror telescope in the world. And just in case you are curious: No, we have never broken a mirror.
What are the advantages of observatories here on Earth over space telescopes?
The GMT as a next-generation extremely large telescope will have a diameter of 25 meters – the size of a basketball court. It will see 10 times better than the Hubble Space Telescope and four times better than the James Webb Space Telescope. Telescopes allow astronomers to see objects in the universe as they appeared when the light that is reaching our telescope today left them. For objects that are billions of light-years away, that means we see them as they appeared billions of years ago. And the larger the telescope, the further back in time we can see. Upgrading or fixing a telescope in space can be very expensive, if even possible at all. The JWST is 1 million miles away from Earth. There's no way we could go out there and repair something. Ground-based telescopes, on the other hand, can be updated as new technology or different instrumentation become available.
What's something that makes you love working at the Mirror Lab?
I've been with the Mirror Lab since 2009, when I was tasked with creating outreach tours for the general public. It is fun to explain to people a very complicated process and to see their amazement about what we do here. The fact that they can see something that they can't see anyplace else in the world makes it a unique experience for them. And while we currently aren't offering any public tours, we are working on restarting that program as soon as possible.