Sixth Mirror Casting Brings Giant Magellan Telescope Closer to Completion
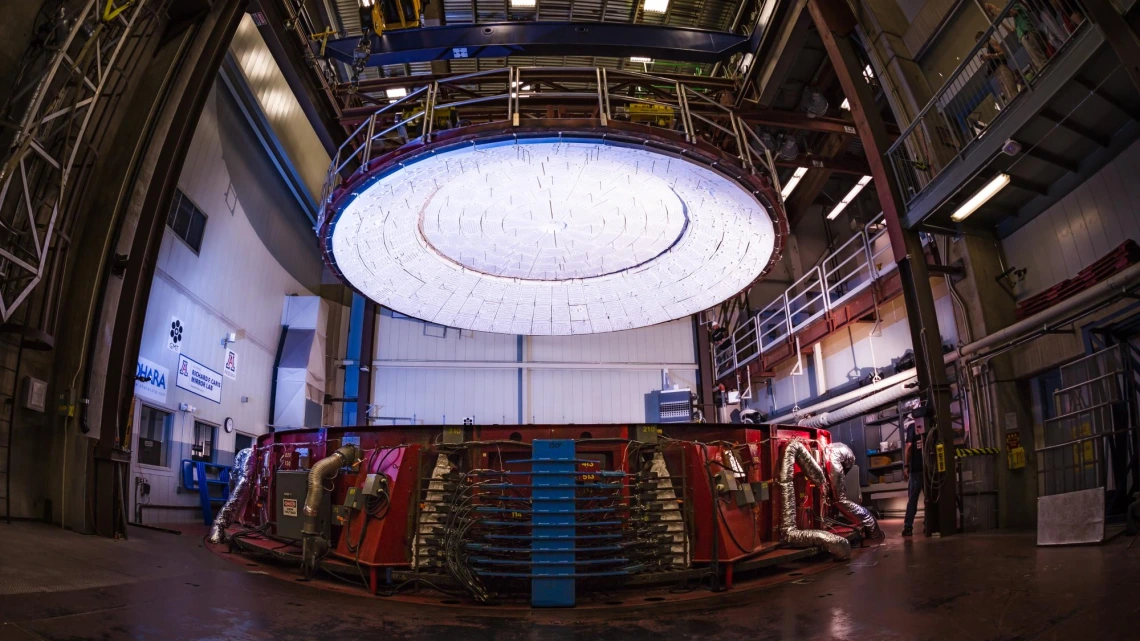
Underneath the stands of the Arizona Wildcats Football Stadium, engineers of UArizona's Richard F. Caris Mirror Lab manufacture the world's largest and most lightweight telescope mirrors. At the center of the process is a giant spinning furnace, the only one of its kind.
Damien Jemison, Giant Magellan Telescope – GMTO Corporation
At 3 p.m. on March 5, a gigantic furnace will slowly start spinning underneath the stands of Arizona Stadium at the University of Arizona. Fire-engine red, massive in size and resembling a sci-fi version of a Dutch oven, the furnace is the only one of its kind, and its sole purpose is to produce the world's biggest and most advanced telescope mirrors.
During the process, nearly 20 tons (17.5 metric tons) of extremely pure borosilicate glass made by Ohara Corporation in Japan will become a honeycomb mirror measuring 27.6 feet (8.4 meters) across. The mirror is the sixth of seven segments that together will make up the primary mirror of the Giant Magellan Telescope, currently under construction in Chile's Atacama Desert. The telescope will see farther into the universe and capture more detail than any optical telescope before.
Arranged in a flower-like array, seven individual mirror segments will come together to form a primary mirror surface measuring 82 feet (25 meters) in diameter. Due to the primary mirror's large size and deep curvature, the shape of each outer segment is unlike any mirror ever made and required major innovations for polishing and measuring the surface.
Spin-casting is the first step of a four-year process to create each mirror. The other steps are carried out in other parts of the Mirror Lab, so up to four mirror segments can be manufactured in parallel.
"The spin-casting is undeniably the most spectacular part of the manufacturing process," said Buddy Martin, polishing scientist at the university's Richard F. Caris Mirror Lab. Martin explained that after the casting, the surface "roughness" is about 2.5 millimeters, or a tenth of an inch, on average.
"The polishing and constant measuring are what turn this amazing piece of glass into a mirror," he said. "By the time we finish polishing, it will be accurate to better than 25 nanometers. That's how smooth the surface has to be in order to make the sharpest possible images."
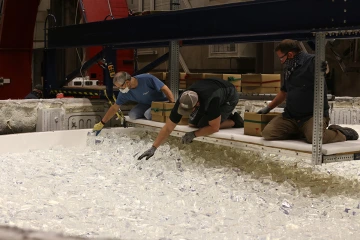
Engineers at the Richard F. Caris Mirror Lab hand-load chunks of glass into the mold. Almost 20 tons of glass are added this way before the lid will be closed and the furnace fired up to melt the glass.
Richard F. Caris Mirror Lab, The University of Arizona
Glass That Flows Like Honey
It took engineers and technicians four months to build the mold that will form the sixth lightweight honeycomb mirror, and it took nine hours to cover the mold with glass. With the mold in place and the glass loaded, they closed the furnace's lid, which measures 33 feet (10 meters) in diameter.
The furnace began heating the glass on March 1 and will reach a peak temperature of 2,129 degrees Fahrenheit (1,165 degrees Celsius) at 2 p.m. on March 6. The day prior, the furnace will begin rotating at five revolutions per minute, so as the glass melts, it is forced outward and up the sides of the mold to form a curved surface. At peak temperature, the glass will take on the consistency of honey and slowly flow into the mold to form the honeycomb structure.
The mirror will then enter a monthlong "annealing" process, during which the molten glass will cool while the furnace spins at a slower rate in order to remove internal stresses and toughen the glass. During this period, the mirror must have a uniform temperature, which is achieved by cooling it very slowly for just over a month. It will take another month and a half to cool to room temperature. Once the mold has been removed, the mirror "blank" will then be ready for grinding and polishing to refine the surface.
Viewing Power 10 Times Greater Than Hubble
With the first two giant mirrors completed and placed in storage in Tucson, the sixth mirror joins three others in various stages of production at the Mirror Lab. The third mirror's front surface polishing process is less than a year from completion. The fourth mirror has completed rear surface polishing, and load spreaders are being attached to allow the mirror to be manipulated during operation. The fifth mirror was cast in November 2017, and the seventh mirror is expected to be cast in 2023. An eighth mirror segment will also be made and can be swapped in when another segment requires maintenance.
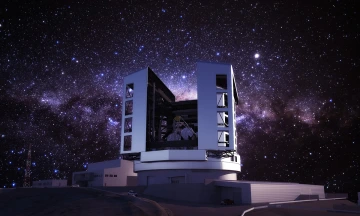
The mirror about to be cast this week is the sixth of seven segments that together will make up the primary mirror of the Giant Magellan Telescope, currently under construction in Chile's Atacama Desert. The telescope will see farther into the universe and capture more detail than any optical telescope before.
Giant Magellan Telescope – GMTO Corporation
Once the Giant Magellan Telescope becomes fully operational, it will have a light collecting area of 3,961 square feet (368 square meters) – enough to see the torch engraved on a dime from nearly 100 miles away. It also will offer the widest field of view of any Extremely Large Telescope in the 30-meter (98-foot) class. The telescope's viewing power is 10 times greater than the famed Hubble Space Telescope and four times greater than the highly anticipated James Webb Space Telescope, expected to launch in late 2021.
In the late 2020s, the giant mirrors will be transported more than 5,000 miles to the Giant Magellan Telescope's future home at Las Campanas Observatory more than 8,000 feet (2,400 meters) above sea level. The site is known for being one of the best astronomical sites on the planet, with its clear skies, low light pollution and stable airflow. The southern hemisphere location allows the telescope to see the Milky Way's center, which is of great scientific interest because of the types of stars found there and the super-massive black hole that lies at the center of the galaxy.
UArizona's Richard F. Caris Mirror Lab has been making the world's most advanced telescope mirrors for almost 40 years, and for the last 24 years has made the world's largest mirrors. These unique mirrors are lightweight honeycomb structures with the ideal mechanical and thermal properties needed to hold their shape to an accuracy of 50 nanometers (2 millionths of an inch) through thousands of nights of telescope observations.
Each mirror casting is a marvel of modern engineering that is usually celebrated with a large in-person event with attendees from around the world. Due to the COVID-19 pandemic, the sixth mirror segment will be cast behind closed doors to protect the health of the 10-person mirror casting team.
The Giant Magellan Telescope project is the work of a distinguished international consortium of leading universities and science institutions. For more information about the Giant Magellan Telescope, visit gmto.org.