Testing begins at U of A for Giant Magellan Telescope's high-tech mirror support structure
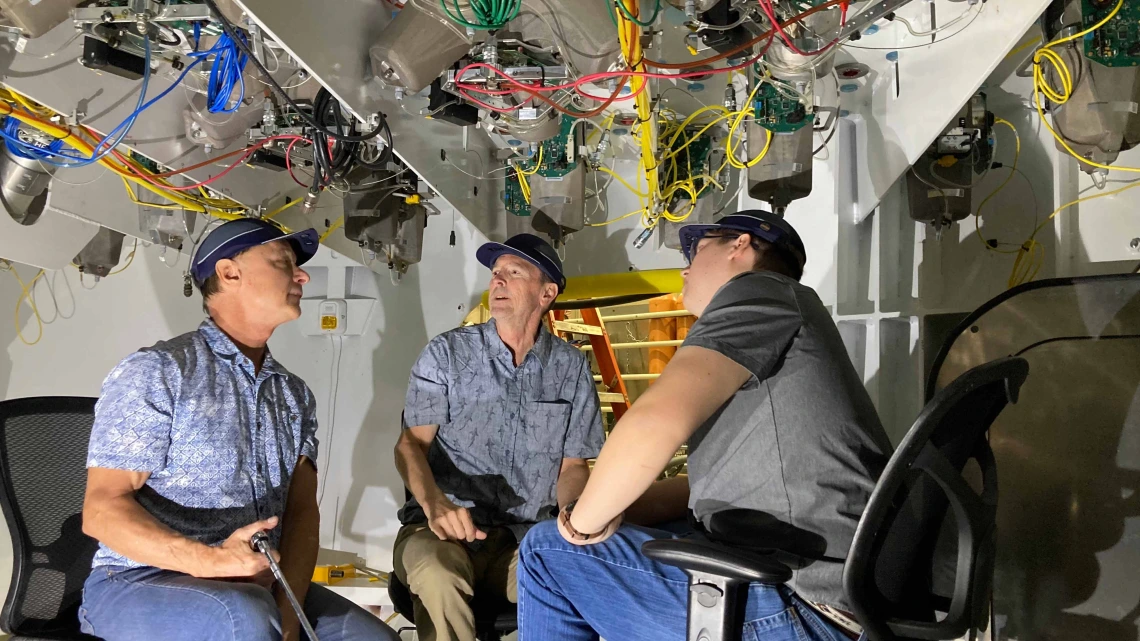
Buddy Martin (center) inspects components inside the support cell with Giant Magellan Telescope engineers Tomas Krasuski (left) and Colby Gottschalk (right).
Daniel Stolte/University Communications
Inside the Richard F. Caris Mirror Lab underneath the University of Arizona football stadium, a giant glass mirror covered in a blue, translucent protective coating rests on a hollow steel platform painted white. Engineers and technicians duck as they enter and exit the structure to check on wires, electrical connections and various mechanical hardware components.
Spanning 28 feet in diameter, the mirror is one of seven segments that together will make up the primary mirror for the Giant Magellan Telescope, currently under construction in the Atacama Desert in Chile. The Giant Magellan's 368-square-meter light-collecting surface is composed of the world's largest optical mirrors, arranged in a unique flower pattern. Together, they will provide the highest image resolution over the widest field of view ever achieved for the exploration of the universe – delivering up to 200 times the power of today's best telescopes.
Each primary mirror weighs 16 metric tons and is supported by a highly specialized pneumatic support system, which is housed in a steel weldment, or "cell." This system works with nanometer precision and is designed to adjust the mirror's position, stabilize its temperature, protect it from seismic activity, and maintain its precise shape by mitigating mirror sagging from gravity as the telescope moves. The system controls the combined seven primary mirrors to act as a single light-collecting surface, creating the optimal conditions for peak optical performance during scientific observations.

Suspended by suction cups, one of the Giant Magellan Telescope's seven primary mirror segments is hoisted onto its support structure by a crane at the Richard F. Caris Mirror Lab.
GMTO Corporation
The mirror used for testing the support structure sits on 160 so-called actuators, which are spaced out evenly across the surface of the steel platform underneath. This highly sophisticated system – comparable in size to half a basketball court and containing three times the number of parts of a typical car – is vital to the telescope's optical performance and precision control. Controlled by computers and using pneumatic controls, the actuators act in concert to compensate for the tiny deformations the mirror segment will experience when exposed to gusts of wind, temperature changes and being moved and tilted during a typical observing night.
Now that one of the primary mirrors has been successfully integrated with the support system prototype, it will undergo rigorous testing under a metrology tower at the Richard F. Caris Mirror Lab to confirm that the mirror can maintain its shape and performance under various operational conditions. Ultra-precise lasers will measure how well the actuators between the support structure and the mirror perform to keep the mirror's surface accurate to a millionth of an inch under the conditions it will experience mounted on the telescope in Chile. Once testing is complete, the design for the production active support systems will undergo a final design review, and production will commence in 2027.
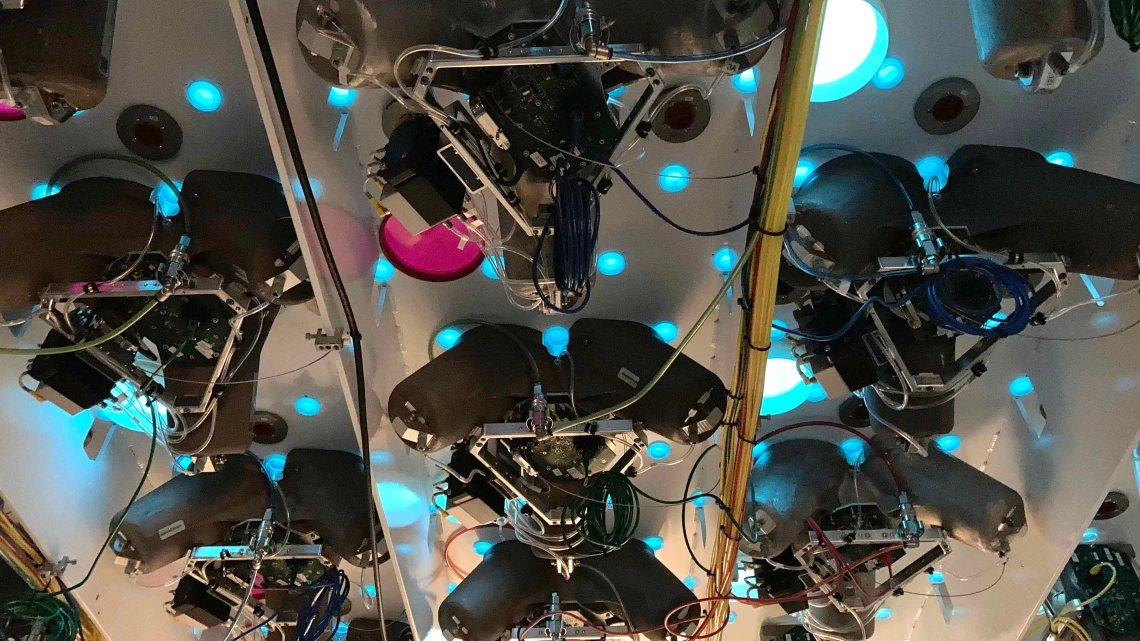
An array of actuators (black cylindrical devices) connects the support structure with the telescope mirror resting on top of it. Using a sophisticated choreography of computer-controlled movements, the actuators work in concert to maintain the mirror’s precise shape while it is moved and tilted by the telescope and buffeted by wind gusts.
Daniel Stolte/University Communications
The milestone marks the start of a six-month optical testing phase to demonstrate that the support system can control the mirror as required, validating the revolutionary capabilities of the telescope's primary light-collecting surface.
"This is the first time this large and complex mirror support system has been built, and this is the one and only opportunity to test it in the lab," said Buddy Martin, who oversees mirror polishing and testing at the Mirror Lab. "By having a GMT segment on the support system and controlling its shape with the actuators, we can test the system's performance to the same accuracy that we used to evaluate the mirror during polishing – one millionth of an inch."
Funded by a National Science Foundation award, the work of integrating the active support prototype system began more than three years ago. Initially, a steel mirror mass simulator acting as a stand-in for the actual mirror was used to demonstrate that the design was able to safely support and control the completed primary mirror segments.
As a key part of the integration process, the Giant Magellan Telescope Organization worked closely with Texas A&M University to clean, assemble and test the support actuators that are being used in the cell. The test cell components were then assembled at the U of A Tech Park. While the actual installation of the mirror into the cell took only one day, the process began with four weeks of disassembly to prepare the cell and support system for transport. The system was then moved 20 miles from the Tech Park to the Mirror Lab for reassembly. This logistically complex operation occurred a few hours after midnight to minimize traffic disruptions, as the wide-load cell required two road lanes for transport.
"This intricate system took years of designing, building, and testing by a team of specialized engineers and technicians," said Tomas Krasuski, principal software and system test engineer for the Giant Magellan Telescope. "Every single component was thoroughly tested before integrating it into the system. Now that we've installed the mirror segment, we are excited to validate its performance."
The milestone highlights the next stage of advancement for the Giant Magellan Telescope's seven primary mirror segments and their support systems. Three of the primary mirror segments are complete, while the remaining four are in various stages of manufacture. The seventh and final primary mirror was cast in October 2023 and is now being prepared for polishing. This latest milestone also follows the August 2024 start of the Giant Magellan's 39-meter-tall telescope mount structure assembly at Ingersoll Machine Tools in Rockford, Illinois. The mount will support the seven primary mirror segments and their cells, adaptive optics and scientific instruments.
The integration of a completed primary mirror segment into its support system is a giant step in the telescope's journey toward first light, according to Giant Magellan Telescope project manager William Burgett. The telescope is now 40% under construction across 36 states and on track to be operational in Chile by the early 2030s.